Following our previous episode with Tobias Richter, we continue exploring the world of dental implants - this time from the perspective of custom solutions and digital workflows. Our guest, Jay Kim, VP of Business Relations and Education at TruAbutment, brings over 16 years of industry experience and shares fascinating insights into the evolution of custom abutments and digital dentistry.
Listen on Spotify
From Dental Novice to Industry Innovator
Jay Kim's journey in dentistry began about 17 years ago when he was scouted by TruAbutment's current CEO. "I didn't know how to spell implants at that time," Kim recalls with candor. "I didn't know anything about dentistry and everything was so intriguing."
His early ventures included launching Denka, a pioneering concept in 3D-printed dentures, approximately 14 years ago. "When we told other people that we were printing dentures, they spat out our faces and thought we were lying," Kim shares.
The Evolution of Custom Abutments
TruAbutment has transformed from a lab business into a comprehensive solutions provider, offering:
- Custom prosthetic solutions
- The URIS implant line
- Digital workflow software
- Educational resources
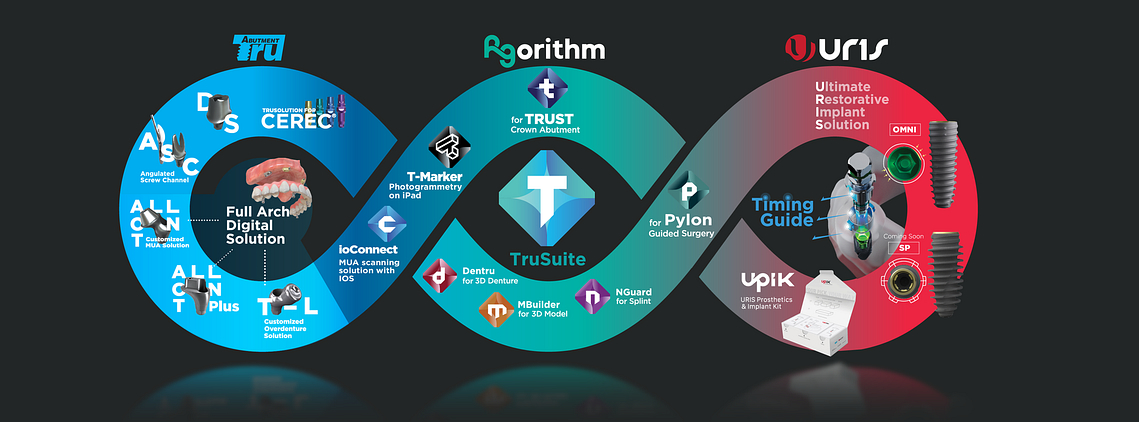
Perhaps the most significant change has been in pricing. "About nine years ago when we launched our custom abutment solution, the median and average price for a custom abutment was still very expensive," Kim explains. Custom abutments previously cost around $500, with final bills to doctors reaching $700-800 for a single unit.
TruAbutment disrupted the market by introducing custom abutments at $180. Today, the market average has settled around $200, while T-bases typically cost between $60-80.
TruAbutment T-base
Manufacturing Innovation
What sets TruAbutment apart is their use of CNC Swiss-type machines, technology typically used in aerospace and implant manufacturing. "We're able to get down the accuracy of that connection and that abutment within five microns of accuracy," Kim states.
This manufacturing approach allows them to produce 110-120 custom abutments per machine daily, a significant advancement that helped make custom solutions more accessible.
CNC Swiss-type milling machine
Digital Workflow Solutions
IO Connect
This innovative solution addresses a fundamental challenge in full-arch scanning.
"The first field of view for a scanner is the most accurate," Kim explains. IO Connect consolidates scan bodies into one position, allowing capture within the first field of view and reducing potential scanning discrepancies.
T-Markers
Set to launch in early 2024, T-Markers represents a new approach to implant verification using iPad technology. The system achieves accuracy levels of 30-40 microns, challenging traditional assumptions about required precision levels.
TruSuite Software
TruAbutment offers several free software solutions through their TruSuite service:
- Pylon: A treatment planning software based on Dentiq, without export fees
- Trust: Their prosthetic design software incorporating AI
"The number one goal right now is data," Kim explains regarding their free software strategy. This data collection supports their AI development and future innovations.
Future of Digital Dentistry
Kim sees significant developments on the horizon, particularly in 3D printing. "If you could print titanium on a five micron level or a 10 micron level, then you print your own implants. You don't need to buy implants, you don't need to mill out custom abutments," he explains.
He also hints at future developments, including the possibility of turning iPads or iPhones into intraoral scanners through specialized adapters.
Looking Ahead
Full arch solutions and 3D printing materials are expected to be major focuses at the upcoming IDS. "You'll see a lot of different solutions come out for full arch because full arch is a very hot topic right now," Kim predicts.
Key Takeaways
- Custom abutment manufacturing has evolved significantly, with prices becoming increasingly competitive
- Digital workflows continue to become more accessible and integrated
- Open architecture solutions drive innovation
- The future of dental manufacturing may lie in advanced 3D printing capabilities
Stay tuned for more episodes of Digital Dentistry Decoded, where we continue to explore the latest developments in digital dentistry.