Over the past few years, we have witnessed significant advancements in 3D-printed bite splints, with numerous resin types entering the market.
However, a persistent challenge with this workflow has been achieving a glossy surface finish akin to traditional analog bite splints that may be milled or thermo-formed.
Manual polishing 3D printed splints often fail to deliver the same high-gloss finish, and chemical polishing methods, such as light-cured glazes, have a tendency to deteriorate over time or crack.
One popular method to achieve a high-gloss finish on printed materials is called the "Candy Coating" technique.
This is basically adding an extra layer of the same resin (used for the bite splint) to the surface of the prosthetic.
This is thinly applied and cured without any further touches. This is done after the splint has been printed and briefly processed. Check out the video at the top of the page for the entire workflow:
A video by Dr Wally Renne was first published on YouTube but this is our own take on the method he showed.
While trying to replicate what he did in our workflow, we found it difficult to achieve a smooth surface without some post-processing as (depending on the resin) printing usually results in a few leftover connectors or nubs.
So this is our take on the “Candy Coat” method.
We added a few extra steps to the technique so you too, can also learn how to achieve shiny 3D splints below.
Step 1: 3D Printing the Splint
At the iDD lab, we used an Asiga MAX UV printer and Keysplint Soft by Keystone Industries printing resin for this example.
In our experience, this resin is by far the best for printed splints at the moment.
It is recommended to nest the splint at a 30 to 45-degree angle to the build platform with the intaglio surface facing away from the build platform. Use the printing software to generate automatic supports as required.
Check if any of the supports are interfering with the intaglio surface of the splint, if so, remove them before printing.
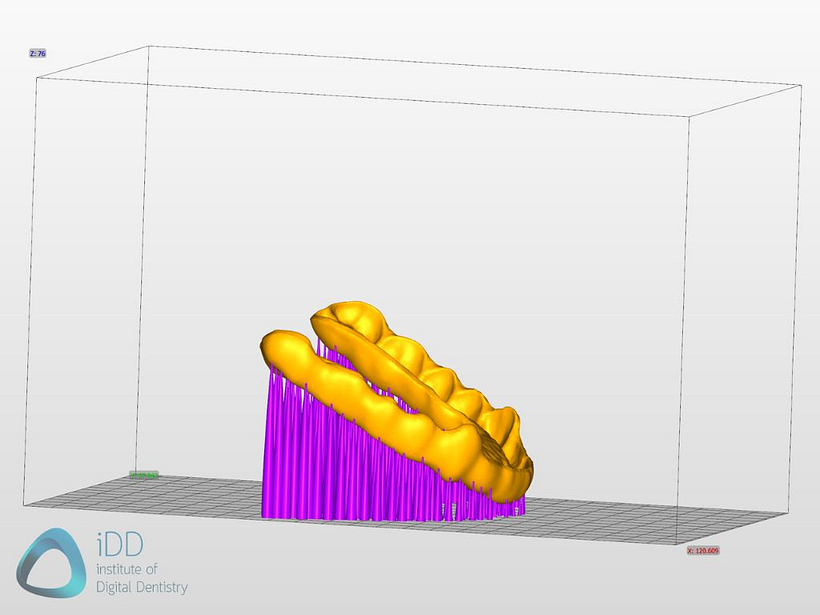
Bite splint with supports ready for 3D printing in Asiga’s slicing software (Asiga Composer). It is recommended to position the splint at a 30 to 45-degree angle to the build platform with the intaglio surface facing away from the build platform. Alternatively print it flat.
Step 2: Post-Processing the Splint - Cleaning
After about three and a half hours of printing (printing time varies from printed to printer), remove the bite splint from the platform and start cleaning.
Most of the printing supports come off very easily by hand, but some may require the use of pliers for removal.
Once this is all done, put the splint in a container with clean isopropyl alcohol and brush off any excess resin. Let the splint soak for about five minutes, then remove and air dry, using pressurized air if you can.
Most of the supports can be easily removed by hand with KeySplint Soft resin.
Step 3: Post-Processing the Splint - Polishing
Take the splint to the workbench and remove the remaining supports or any type of irregularity on the surface of the splint using burs or silicone polishers.
Be careful while doing so to avoid modifying the occlusal contacts that were designed in the splint CAD process.
Use a lathe/polishing wheel to achieve a smooth and more uniform surface. This step is no different than polishing a traditional acrylic night guard.
After polishing, wash the splint under running water and dry it well. It’s crucial that the splint surface is clean, dry, and smooth before adding an extra layer of resin in the Candy Coat technique.
Remove and refine the surface of the splint using burs or silicone polishers.
Step 4: Candy Coating the Splint
To Candy Coat - you will need a container with the same resin that was used to print the splint and a brush to apply this resin gain to the surface.
Apply the resin in a very thin layer - we cannot stress this enough. Do not lather it on so that it does not interfere with the overall shape or fit of the splint.
You can apply the resin to the intaglio and perform a quick cure with a handpiece curing light to avoid resin dripping as you turn it over to apply it all over. Apply the resin on the outside of the splint and the inside. Apply gently and with patience, to ensure the entirety of the surface is covered.
Cure the applied resin to prevent it from dripping while carrying out the technique.
Step 5: Curing the Splint
Carefully place the splint in a transparent container (we used a plastic food container) and place it inside a curing machine. Ensure that your curing box uses the right wavelength of light for the resin you are using.
In this case we used SprintRay Pro Cure 2, which already has the presets for the KeySplint resin pre-loaded and can be chosen. The curing time is set at around five minutes and twenty-three seconds.
Note that each resin will have a different preset or required setting. Remember to always follow the manufacturer's recommendations and do not over-cure the resin because it can cause the material to become too brittle or change color.
Now comes the important part: halfway through the curing cycle, stop the curing unit, remove the splint, and submerge it in glycerin to counteract the oxygen inhibition layer.
What is this layer? Oxygen in the air interferes with the polymerization of the very topmost layer of any resin, so placing it in glycerin prevents this from happening. If you do not do this, you cannot guarantee your resin splint is biocompatible.
After finishing the full cure cycle, wash the splint in running water and dry.
And there you have it! A completed splint using the modified Candy Coating technique.
Halfway through the curing cycle, put the splint in glycerin to prevent the oxygen inhibition layer from forming, otherwise you cannot guarantee the biocompatibility of the material.
Applications of the Candy Coat Technique
Interestingly, this method can be applied not only for splints and nightguards but to any printed resin, so you can even give it a shot with printed dentures, for instance.
You can either try it using the same resin or using a clear biocompatible resin as the final extra candy-coating layer.
So, what are your thoughts? Does it require too much work or is it worth it for the nice shiny results?
Let us know in the comments below if you’ll be applying this technique with your splint workflow from now on.
A 3D printed bite splint finished with the Candy Coating technique.
Want to learn more?
Join Marjorie Andrade to learn how to Master exocad and get the most out of the software.
The course Modules range from fundamental topics like setting up the software and designing basic crowns…
All the way to advanced material like full-mouth rehabilitation and implant planning.
Hello
I tried the candy Coating on a bite split many times
I have a 2 problems :
It takes one hour and 30 mins in the light cure and still sticky
Smoll air bubbles after I cure it in the glycerol.
I have a formlab curing box:
Form cure
Using keysplint soft clear
Do u have any advice to solve my problems?
Best regards
Hey there
Here is my advice – Formlab’s old cure box (if you are using that) is not powerful enough. You may need a better one.
Also only cure for 1 minute with high power. Before curing dont touch the surface at all after candy coating and even after the initial cure. Then gently put in the glycerol, and cure for 2-3 minutes.